Metals get softer when they are heated, which is how blacksmiths can form iron into complex shapes by heating it red hot. And anyone who compares a copper wire with a steel coat hanger will quickly discern that copper is much more pliable than steel.
But scientists at MIT have discovered that when metal is struck by an object moving at a super high velocity, the opposite happens: The hotter the metal, the stronger it is. Under those conditions, which put extreme stress on the metal, copper can actually be just as strong as steel. The new discovery could lead to new approaches to designing materials for extreme environments, such as shields that protect spacecraft or hypersonic aircraft, or equipment for high-speed manufacturing processes.
The findings are described in a paper appearing today in the journal Nature, by Ian Dowding, an MIT graduate student, and Christopher Schuh, former head of MIT’s Department of Materials Science and Engineering, now dean of engineering at Northwestern University and visiting professor at MIT.
The new finding, the authors write, “is counterintuitive and at odds with decades of studies in less extreme conditions.” The unexpected results could affect a variety of applications because the extreme velocities involved in these impacts occur routinely in meteorite impacts on spacecraft in orbit and in high-speed machining operations used in manufacturing, sandblasting, and some additive manufacturing (3D printing) processes.
The experiments the researchers used to find this effect involved shooting tiny particles of sapphire, just millionths of a meter across, at flat sheets of metal. Propelled by laser beams, the particles reached high velocities, on the order of a few hundred meters per second. While other researchers have occasionally done experiments at similarly high velocities, they have tended to use larger impactors, at the scale of centimeters or larger. Because these larger impacts were dominated by effects of the shock of the impact, there was no way to separate out the mechanical and thermal effects.
The tiny particles in the new study don’t create a significant pressure wave when they hit the target. But it has taken a decade of research at MIT to develop methods of propelling such microscopic particles at such high velocities. “We’ve taken advantage of that,” Schuh says, along with other new techniques for observing the high-speed impact itself.
The team used extremely high-speed cameras “to watch the particles as they come in and as they fly away,” he says. As the particles bounce off the surface, the difference between the incoming and outgoing velocities “tells you how much energy was deposited” into the target, which is an indicator of the surface strength.
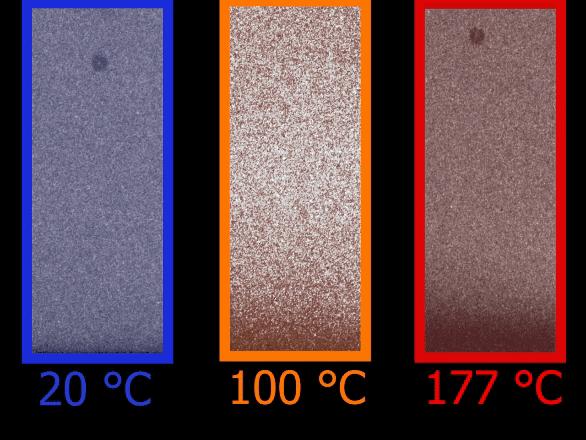

The tiny particles they used were made of alumina, or sapphire, and are “very hard,” Dowding says. At 10 to 20 microns (millionths of a meter) across, these are between one-tenth and one-fifth of the thickness of a human hair. When the launchpad behind those particles is hit by a laser beam, part of the material vaporizes, creating a jet of vapor that propels the particle in the opposite direction.
The researchers shot the particles at samples of copper, titanium, and gold, and they expect their results should apply to other metals as well. They say their data provide the first direct experimental evidence for this anomalous thermal effect of increased strength with greater heat, although hints of such an effect had been reported before.
The surprising effect appears to result from the way the orderly arrays of atoms that make up the crystalline structure of metals move under different conditions, according to the researchers’ analysis. They show that there are three separate effects governing how metal deforms under stress, and while two of these follow the predicted trajectory of increasing deformation at higher temperatures, it is the third effect, called drag strengthening, that reverses its effect when the deformation rate crosses a certain threshold.
Beyond this crossover point, the higher temperature increases the activity of phonons — waves of sound or heat — within the material, and these phonons interact with dislocations in the crystalline lattice in a way that limits their ability to slip and deform. The effect increases with increased impact speed and temperature, Dowding says, so that “the faster you go, the less the dislocations are able to respond.”
Of course, at some point the increased temperature will begin to melt the metal, and at that point the effect will reverse again and lead to softening. “There will be a limit” to this strengthening effect, Dowding says, “but we don’t know what it is.”
The findings could lead to different choices of materials when designing devices that may encounter such extreme stresses, Schuh says. For example, metals that may ordinarily be much weaker, but that are less expensive or easier to process, might be useful in situations where nobody would have thought to use them before.
The extreme conditions the researchers studied are not confined to spacecraft or extreme manufacturing methods. “If you are flying a helicopter in a sandstorm, a lot of these sand particles will reach high velocities as they hit the blades,” Dowding says, and under desert conditions they may reach the high temperatures where these hardening effects kick in.
The techniques the researchers used to uncover this phenomenon could be applied to a variety of other materials and situations, including other metals and alloys. Designing materials to be used in extreme conditions by simply extrapolating from known properties at less extreme conditions could lead to seriously mistaken expectations about how materials will behave under extreme stresses, they say.
The research was supported by the U.S. Department of Energy.