Metamaterials are products of engineering wizardry. They are made from everyday polymers, ceramics, and metals. And when constructed precisely at the microscale, in intricate architectures, these ordinary materials can take on extraordinary properties.
With the help of computer simulations, engineers can play with any combination of microstructures to see how certain materials can transform, for instance, into sound-focusing acoustic lenses or lightweight, bulletproof films.
But simulations can only take a design so far. To know for sure whether a metamaterial will stand up to expectation, physically testing them is a must. But there’s been no reliable way to push and pull on metamaterials at the microscale, and to know how they will respond, without contacting and physically damaging the structures in the process.
Now, a new laser-based technique offers a safe and fast solution that could speed up the discovery of promising metamaterials for real-world applications.
The technique, developed by MIT engineers, probes metamaterials with a system of two lasers — one to quickly zap a structure and the other to measure the ways in which it vibrates in response, much like striking a bell with a mallet and recording its reverb. In contrast to a mallet, the lasers make no physical contact. Yet they can produce vibrations throughout a metamaterial’s tiny beams and struts, as if the structure were being physically struck, stretched, or sheared.
The engineers can then use the resulting vibrations to calculate various dynamic properties of the material, such as how it would respond to impacts and how it would absorb or scatter sound. With an ultrafast laser pulse, they can excite and measure hundreds of miniature structures within minutes. The new technique offers a safe, reliable, and high-throughput way to dynamically characterize microscale metamaterials, for the first time.
“We need to find quicker ways of testing, optimizing, and tweaking these materials,” says Carlos Portela, the Brit and Alex d’Arbeloff Career Development Professor in Mechanical Engineering at MIT. “With this approach, we can accelerate the discovery of optimal materials, depending on the properties you want.”
Portela and his colleagues detail their new system, which they’ve named LIRAS (for laser-induced resonant acoustic spectroscopy) in a paper appearing today in Nature. His MIT co-authors include first author Yun Kai, Somayajulu Dhulipala, Rachel Sun, Jet Lem, and Thomas Pezeril, along with Washington DeLima at the U.S. Department of Energy’s Kansas City National Security Campus.
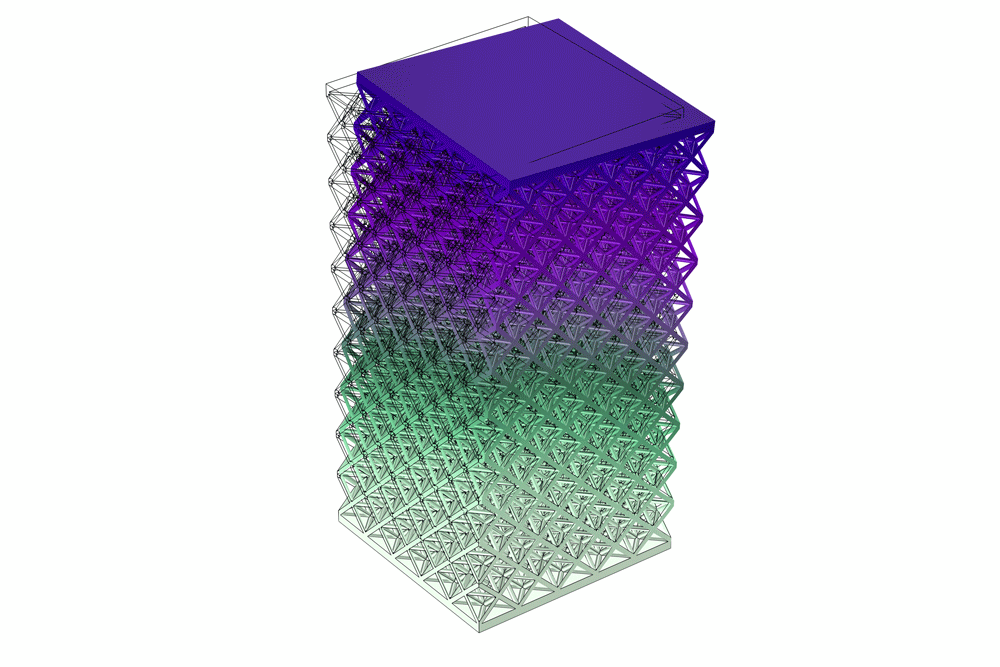
A slow tip
The metamaterials that Portela works with are made from common polymers that he 3D-prints into tiny, scaffold-like towers made from microscopic struts and beams. Each tower is patterned by repeating and layering a single geometric unit, such as an eight-pointed configuration of connecting beams. When stacked end to end, the tower arrangement can give the whole polymer properties that it would not otherwise have.
But engineers are severely limited in their options for physically testing and validating these metamaterial properties. Nanoindentation is the typical way in which such microstructures are probed, though in a very deliberate and controlled fashion. The method employs a micrometer-scale tip to slowly push down on a structure while measuring the tiny displacement and forces on the structure as it’s compressed.
“But this technique can only go so fast, while also damaging the structure,” Portela notes. “We wanted to find a way to measure how these structures would behave dynamically, for instance in the initial response to a strong impact, but in a way that would not destroy them.”
A (meta)material world
The team turned to laser ultrasonics — a nondestructive method that uses a short laser pulse tuned to ultrasound frequencies, to excite very thin materials such as gold films without physically touching them. The ultrasound waves created by the laser excitation are within a range that can cause a thin film to vibrate at a frequency that scientists can then use to determine the film’s exact thickness down to nanometer precision. The technique can also be used to determine whether a thin film holds any defects.
Portela and his colleagues realized that ultrasonic lasers might also safely induce their 3D metamaterial towers to vibrate; the height of the towers — ranging from 50 to 200 micrometers tall, or up to roughly twice the diameter of a human hair — is on a similar microscopic scale to thin films.
To test this idea, Yun Kai, who joined Portela’s group with expertise in laser optics, built a tabletop setup comprising two ultrasonic lasers — a “pulse” laser to excite metamaterial samples and a “probe” laser to measure the resulting vibrations.
On a single chip no bigger than a fingernail, the team then printed hundreds of microscopic towers, each with a specific height and architecture. They placed this miniature city of metamaterials in the two-laser setup, then excited the towers with repeated ultrashort pulses. The second laser measured the vibrations from each individual tower. The team then gathered the data, and looked for patterns in the vibrations.
“We excite all these structures with a laser, which is like hitting them with a hammer. And then we capture all the wiggles from hundreds of towers, and they all wobble in slightly different ways,” Portela says. “Then we can analyze these wiggles and extract the dynamic properties of each structure, such as their stiffness in response to impact, and how fast ultrasound travels through them.”
The team used the same technique to scan towers for defects. They printed several defect-free towers and then printed the same architectures, but with varying degrees of defects, such as missing struts and beams, each smaller than the size of a red blood cell.
“Since each tower has a vibrational signature, we saw that the more defects we put into that same structure, the more this signature shifted,” Portela explains. “You could imagine scanning an assembly line of structures. If you detect one with a slightly different signature, you know it’s not perfect.”
He says scientists can easily recreate the laser setup in their own labs. Then, Portela predicts the discovery of practical, real-world metamaterials will take off. For his part, Portela is keen to fabricate and test metamaterials that focus ultrasound waves, for instance to boost the sensitivity of ultrasound probes. He’s also exploring impact-resistant metamaterials, for instance to line the inside of bike helmets.
“We know how important it is to make materials to mitigate shock and impacts,” Kai offers. “Now with our study, for the first time we can characterize the dynamic behavior of metamaterials and explore them to the extreme.”
This research was conducted, in part, using facilities at MIT.nano, and supported, in part, by the Department of Energy’s Kansas City National Security Campus, the National Science Foundation, and DEVCOM ARL Army Research Office through the MIT Institute of Soldier Nanotechnologies.