Carbon nanotubes can contribute their mechanical strength and electrical properties across a wide range of areas from aerospace to medicine, and the necstlab of MIT Associate Professor of Aeronautics and Astronautics Brian L. Wardle is making an impact in deicing, polymer composites and sensors.
Two hallmark technologies, nanostitch architecture and fuzzy fiber architecture, underlie advances in mechanical strength for aerospace with lighter weight and low power anti-icing for airplane wings. Both use aligned nanowires, specifically carbon nanotube forests, which are compatible with carbon-fiber polymer composites.
"We’ve proven two of these hybrid advanced composite architectures comprised of nanowires plus micron scale advanced fibers, which are carbon fibers in aerospace applications due to their specific strength and their specific stiffness," Wardle says.
Eager to fly
"Our nanocomposite materials also have the attribute that you can control the electrical conductivity and spatially tailor heating, so that it’s been utilized for what’s called an ice protection system (IPS). That technology has been integrated onto wings and gone through several days of full scale ice tunnel testing. It’s actually something I’m quite proud of from the standpoint that I’ve been working with nanomaterials for bulk materials, and now I have wings that have meter scale bars. These are meter-long members being tested in an ice tunnel, and I'll be even happier when they fly," Wardle says.
Video footage shows the carbon nanotubes at work in deicing and anti-icing. First author Samuel T. Buschhorn, a postdoctoral associate, presented the paper, "Electrothermal Icing Protection of Aerosurfaces Using Conductive Polymer Nanocomposites," at the American Institute of Aeronautics and Astronautics conference in Boston in April 2013. Wardle and Lachman were among the co-authors.
The work was done in collaboration with Metis Design Corp. in Boston. Wardle's NECST Consortium has spun off a company, N12 Technologies, for commercializing the technology, and he hopes that early to mid-2014 will see both commercial and unpiloted aerial vehicle (UAV), or drone, testing.
The de-icing uses nanostitch technologies to weld carbon nanotubes to a wing. "We’ve refined the manufacturing and synthesis aspects, so we’re making the materials nearly in the way that I originally envisioned them, and indeed, we’re observing the mechanical property improvements consistent with the models that we have at hand. We’re also learning some new things, these reinforcements are actually giving us strength in the opposite direction, enhancing properties that we did not expect initially, so we are learning as we go along as well," Wardle says.
With the NECST Consortium, graduate student Richard Li and postdoc Stephen Steiner published results of a study of CNTs grown on carbon-fiber in May 2013. Postdoctoral associate Noa Lachman is defining atomic level morphology, or geometric structure, of carbon nanotube forests within macroscopic composites and devices.
"This group is pretty much a team, more than just a group," Lachman says. Ph.D. candidate Sunny Wicks has demonstrated enhanced fracture toughness in aligned CNT-reinforced laminates made with both marine and aerospace epoxies. "The more I work on this material, the more complex it gets," Wicks says.
Improving structural properties
For Wardle, it's all following a strategic plan. "We're after improving the structural properties," he says. In the nanostitch architecture, the carbon nanowires reinforce the interface between layers of polymer composites, and in the fuzzy fiber architecture, they reinforce the bulk of the material. The vertical arrays are knocked down and compressed for the nanostitch deicing application.
"Existing advanced composite materials are widely used in aerospace because they are strong and light as well as stiff and light. We can make advanced materials, which are highly engineered materials, even more advanced by reinforcing areas where they are insufficiently reinforced, with these aligned nanowires. All of our nanomaterials are fiber materials. A typical array has 50 billion nanowires per square centimeter, so there is a lot of reinforcement potential," Wardle says. "Our approach is to do the structural work first and then you get the multi-functional for free." Those extras include enhanced electrical and thermal conductivity. The work is supported by industry and government, including the U.S. Army, Navy and Air Force as well as the National Science Foundation.
"The core of the group going forward is still to investigate and understand the true potential of these architectures that we’re now still demonstrating," Wardle says.
Referring to Li and Steiner's work on CNTs grown on carbon fiber, he says, "One of the exciting things we now have at a very small scale, but a relevant composite scale, is this fuzzy fiber architecture on carbon fiber. It’s very exciting to think about making the larger scale materials, laminate-level versions of fuzzy carbon fibers. That will be a big piece of work in the next couple of years. I’m very excited about the intersection of nanotechnology and manufacturing. So we have several things demonstrated and several programs that will be expanding over the next year. We’re looking at nanotechnologies as a way to improve the effectiveness of manufacturing as well as reduce cost."
One project is to look at reducing the energy used to make carbon fiber composites in ovens. "We have the ability to reduce the amount of energy used by factors of 10, 100, even a 1000 … so I’m very excited about the future," Wardle says.
A recent initiative funded by the Center for Materials Science and Engineering at MIT will combine the efforts of Wardle, Michael Rubner, Robert Cohen and Gareth McKinley at MIT and Mehmet Toner at Harvard to look at layer-by-layer deposition and functionalizing CNT elements in microfluidics by tailoring their porosity and permeability. Other current work is focused on nanomaterials for energy storage and conversion. Past work includes proving that metal oxides, notably zirconia, could act as a catalyst for nanostructures.
Carbon nanotube deicing technologies developed at MIT could be in flight tests as early as next year.
Publication Date:

Caption:
MIT Associate Professor of Aeronautics and Astronautics Brian L. Wardle
Credits:
Photo: Denis Paiste/Materials Processing Center
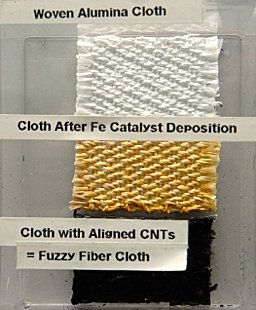
Caption:
From top: Samples of baseline alumina cloth, iron catalyst coated cloth and carbon nanotube strengthened cloth.