As the United States seeks to reinvigorate its job market and move past economic recession, MIT News examines manufacturing’s role in America’s economic future through this series on work at the Institute around manufacturing.
Not long ago, MIT political scientist Suzanne Berger was visiting a factory in western Massachusetts, a place that produces the plastic jugs you find in grocery stores. As she saw on the factory floor, the company has developed an innovative automation system that has increased its business: Between 2004 and 2008, its revenues doubled, and its workforce did, too. Moreover, the firm has found a logical niche: Since plastic jugs are both bulky and inexpensive, it’s not economical to produce them overseas and ship them to the United States, simply to fill them with, say, milk or syrup.
“Is this just an odd little story?” Berger asks. “Actually, no.” While the decline of American manufacturing has been widely trumpeted — manufacturing jobs in the United States have dropped from 20 million in 1979 to about 12 million today — conglomerates such as Procter & Gamble and high-tech firms such as Dow Corning have kept significant amounts of manufacturing in the country. Moreover, 3,500 manufacturing companies across the United States — not just the jug-making firm in Massachusetts — doubled their revenues between 2004 and 2008. With that in mind, Berger asks, “How can we imagine enabling these firms to branch out into more innovative activities as well?”
That is the kind of problem Berger and 19 of her faculty colleagues at MIT are now studying as part of a two-year Institute-wide research project called Production in the Innovation Economy (PIE), which is focused on renewing American manufacturing. The guiding premise of PIE is that the United States still produces a great deal of promising basic research and technological innovation; what is needed is a better sense of how to translate those advances into economic growth and new jobs.
As Berger puts it, “The single most important question in the study is: What kind of manufacturing do we need in order to get full value out of our innovation strengths?”
That question is currently at the forefront of MIT’s concerns as well. Institute President Susan Hockfield is serving as a co-chair of the steering committee of President Barack Obama’s Advanced Manufacturing Partnership (AMP), which in June will give policy recommendations to the White House about renewing American manufacturing. PIE is not a subset of AMP, but arises from similar concerns about applying technology in the national interest.
Made in America in the 21st century
In the course of conducting its research, PIE will issue an interim report later this spring; publish a final report in 2013; create a film on manufacturing; host a lecture series; and issue a working-paper series of research findings from the professors on the team.
The co-chairs of the PIE Commission are Berger, the Raphael Dorman-Helen Starbuck Professor of Political Science, and biologist and Institute Professor Phillip Sharp. Olivier de Weck, who has served as the associate head of the Engineering Systems Division and also holds a dual appointment with the Department of Aeronautics and Astronautics, is serving as PIE’s executive director.
To a significant extent, PIE is modeled on the MIT Commission on Industrial Productivity, a 1980s group that conducted a similarly long-term study on the American economy and wrote the highly influential book Made in America. Published in 1989, Made in America has sold more than 300,000 copies and influenced public discussion about changes needed to improve America’s industrial productivity, such as greater flexibility in production processes and policies to help firms make capital investments.
However, PIE’s research interests differ from those of the Made in America group in substantial ways. The 1980s research project was organized around the performance of U.S. firms in several major industries then experiencing intensified competition, from automakers to consumer electronics companies. PIE focuses on specific questions that may cut across a multitude of industrial sectors, and has organized its work into eight distinct “modules” that cover a diverse set of issues, ranging from the challenges of scaling up small startups to the problems of training workers.
Like IT or not?
In so doing, PIE is also broadly scrutinizing a common assumption of the last quarter-century: that the information technology industry is the basic paradigm for innovation-based manufacturing in the United States. “Some people think we can just do the innovation, and then license and sell and outsource it,” Berger notes. By contrast, she says, “those of us in the PIE study think it’s an open question whether a similar model works elsewhere, particularly in the new emerging-technology areas.”
Information technology companies often have low startup costs covered by venture capital, and their production tasks lend themselves to being handled overseas. But in other areas with advanced-manufacturing potential, such as energy, advanced materials or biotechnology, “you’re going to need far heavier capital investment,” Berger says. It’s not obvious how such companies can best finance the development and commercialization of their products.
One of the PIE modules will also examine the effects of manufacturing — and the loss of manufacturing jobs — on other industries. Manufacturing is widely viewed as an industry that creates additional jobs besides those on the production lines; factories create a need for additional service-industry workers. Additionally, the income earned by manufacturing workers creates demand for still more goods and services.
The factory visits that Berger and her colleagues have been making for PIE underscore that point. On a recent visit to a company that makes equipment pipes and tanks for biotechnology companies, she found that a quarter of the company’s revenue comes from repairing and servicing the equipment. “What we’re discovering is that this connection between manufacturing and services is an integral one,” Berger says. “A set of capabilities is gained in making products that then get redeployed in the service part of a business.”
Ultimately, the PIE researchers may have many more such discoveries ahead of them — and may need them, to help chart the possible paths for new success in manufacturing.
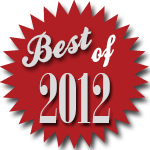
“Is this just an odd little story?” Berger asks. “Actually, no.” While the decline of American manufacturing has been widely trumpeted — manufacturing jobs in the United States have dropped from 20 million in 1979 to about 12 million today — conglomerates such as Procter & Gamble and high-tech firms such as Dow Corning have kept significant amounts of manufacturing in the country. Moreover, 3,500 manufacturing companies across the United States — not just the jug-making firm in Massachusetts — doubled their revenues between 2004 and 2008. With that in mind, Berger asks, “How can we imagine enabling these firms to branch out into more innovative activities as well?”
That is the kind of problem Berger and 19 of her faculty colleagues at MIT are now studying as part of a two-year Institute-wide research project called Production in the Innovation Economy (PIE), which is focused on renewing American manufacturing. The guiding premise of PIE is that the United States still produces a great deal of promising basic research and technological innovation; what is needed is a better sense of how to translate those advances into economic growth and new jobs.
As Berger puts it, “The single most important question in the study is: What kind of manufacturing do we need in order to get full value out of our innovation strengths?”
That question is currently at the forefront of MIT’s concerns as well. Institute President Susan Hockfield is serving as a co-chair of the steering committee of President Barack Obama’s Advanced Manufacturing Partnership (AMP), which in June will give policy recommendations to the White House about renewing American manufacturing. PIE is not a subset of AMP, but arises from similar concerns about applying technology in the national interest.
Made in America in the 21st century
In the course of conducting its research, PIE will issue an interim report later this spring; publish a final report in 2013; create a film on manufacturing; host a lecture series; and issue a working-paper series of research findings from the professors on the team.
The co-chairs of the PIE Commission are Berger, the Raphael Dorman-Helen Starbuck Professor of Political Science, and biologist and Institute Professor Phillip Sharp. Olivier de Weck, who has served as the associate head of the Engineering Systems Division and also holds a dual appointment with the Department of Aeronautics and Astronautics, is serving as PIE’s executive director.
To a significant extent, PIE is modeled on the MIT Commission on Industrial Productivity, a 1980s group that conducted a similarly long-term study on the American economy and wrote the highly influential book Made in America. Published in 1989, Made in America has sold more than 300,000 copies and influenced public discussion about changes needed to improve America’s industrial productivity, such as greater flexibility in production processes and policies to help firms make capital investments.
However, PIE’s research interests differ from those of the Made in America group in substantial ways. The 1980s research project was organized around the performance of U.S. firms in several major industries then experiencing intensified competition, from automakers to consumer electronics companies. PIE focuses on specific questions that may cut across a multitude of industrial sectors, and has organized its work into eight distinct “modules” that cover a diverse set of issues, ranging from the challenges of scaling up small startups to the problems of training workers.
Like IT or not?
In so doing, PIE is also broadly scrutinizing a common assumption of the last quarter-century: that the information technology industry is the basic paradigm for innovation-based manufacturing in the United States. “Some people think we can just do the innovation, and then license and sell and outsource it,” Berger notes. By contrast, she says, “those of us in the PIE study think it’s an open question whether a similar model works elsewhere, particularly in the new emerging-technology areas.”
Information technology companies often have low startup costs covered by venture capital, and their production tasks lend themselves to being handled overseas. But in other areas with advanced-manufacturing potential, such as energy, advanced materials or biotechnology, “you’re going to need far heavier capital investment,” Berger says. It’s not obvious how such companies can best finance the development and commercialization of their products.
One of the PIE modules will also examine the effects of manufacturing — and the loss of manufacturing jobs — on other industries. Manufacturing is widely viewed as an industry that creates additional jobs besides those on the production lines; factories create a need for additional service-industry workers. Additionally, the income earned by manufacturing workers creates demand for still more goods and services.
The factory visits that Berger and her colleagues have been making for PIE underscore that point. On a recent visit to a company that makes equipment pipes and tanks for biotechnology companies, she found that a quarter of the company’s revenue comes from repairing and servicing the equipment. “What we’re discovering is that this connection between manufacturing and services is an integral one,” Berger says. “A set of capabilities is gained in making products that then get redeployed in the service part of a business.”
Ultimately, the PIE researchers may have many more such discoveries ahead of them — and may need them, to help chart the possible paths for new success in manufacturing.